Cavitation
Cavitation
An abundant amount of literature covering the topic of cavitation was published during the 1940s and the 1950s. During this period, the subject received a great deal of attention from both pump and hydraulic turbine manufacturers. This led to an increase in research and development, which resulted in higher pump speeds and safer operation. Today cavitation is still very important to the successful operation of a fluid system and good pump design.
Cavitation is a condition that occurs within a pump. The pumped fluid experiences a local pressure drop, causing portions of the liquid to fill with vapor. This may sound complex, but if you've ever boiled water, you've experienced something very similar to what happens during cavitation. As the water boils, vapor cavities (bubbles) form in the liquid.
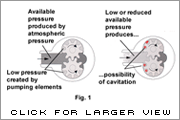
As you know, liquid is not “sucked” into a pump, it is pushed. The liquid being pushed into the pump (available pressure) compensates for the low pressure created by the rapid movement of fluid by the pumping parts. Consequently, when the available pressure is reduced or the local pressure in the pump cavity is low, vapor formation occurs or increases (see Fig. 1).
All fluids form vapor cavities when the pressure on the liquid is reduced to the liquid's vapor pressure at the pumping temperature. These vapor-filled cavities travel through the pump; when the cavities reach regions of relatively high pressure, they collapse. Cavitation damage is caused by the shock waves created when the vapor cavities collapse near the elements in the pump. Cavitation occurs along stationary and moving elements in a pump. For example, the inlet flow hole in a gear pump and the low-pressure side of a gear tooth are places where cavitation could occur. An entire system experiences a drop in available pressure when:
- the fluid must be lifted from a reservoir
- the system is located at a high altitude
- the reservoir is sealed from atmospheric pressure and is under vacuum
- the fluid temperature is relatively high
Cavitation can be identified by four characteristics:
- Noise. A sudden collapse of vapor bubbles creates noisy pump operation.
- Vibration. In severe cases, cavitation causes mechanical shaking.
- Performance. The pressure-flow characteristics of the pump become less than normal during cavitation.
- Material failure. The sudden destructive forces of the collapsing bubbles are powerful enough to cause pitting on the pump body or gear. Cavitation pitting has a distinctly different appearance than corrosion or erosion.
How Do You Spell Relief?
Many methods have been used to combat cavitation. In large centrifugal pumps or valves, admitting air into the inlet provides a cushion for the collapsing bubbles and also reduces the noise and pitting caused by cavitation.
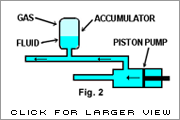
Installing an accumulator (a mechanical device that stores the energy of fluid under pressure) close to the inlet port of a piston pump will reduce the effective inlet tubing length, pressurize the inlet, and absorb excess energy (see Fig. 2).
Pitting can be reduced by changing the hardness of the pumping element material or by applying a protective coating; however, these are not long-term solutions to the problem because pitting will attack areas with nicks, scratches, flaws, or sharp corners.
To reduce the undesirable characteristics of cavitation requires an understanding of the interrelationships of system, pump, and liquid. The following techniques have been used to reduce cavitation, but success is dependent upon the application:
- Keep the speed of the fluid low and eliminate abrupt turns, restrictions, or sudden expansions in the system plumbing.
- Provide adequate pressure to the inlet of the pump, especially in applications with warm or hot liquids, thick viscous fluids, evacuated systems, or when the pumped liquid is volatile. Inlet pressures can be increased by raising the reservoir, lowering the pump, reducing the friction losses of the inlet tubing, or cooling the liquid.
- Install a pump with better lifting capabilities.
Solutions to cavitation problems are not simple. System changes in gear pump applications can be expensive, time consuming, or both. In the early stages of a project, the design team, consisting of the user and the pump designer, must combine their knowledge to reduce the likelihood of cavitation within a fluid system.
Find a Distributor
Get a Quote
Find a Product
Headquarters
1402 NE 136th Avenue
Vancouver, WA 98684-0818 USA