Fuel Additive Injection
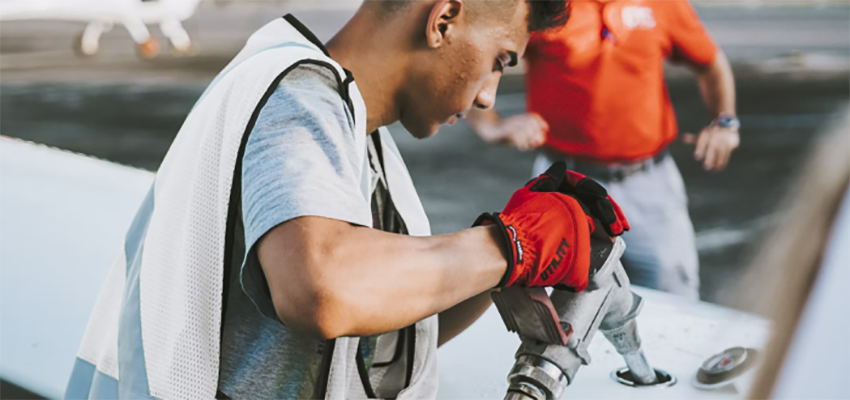
Application-Related Downloads
Application Summary
Application
Fuel Additive Injection
Description
Improving or changing fuel performance by injecting fuel additives
How It’s Used
Pumping a wide variety of fuel additives, at a constant, controlled flow rate, into an injection manifold to facilitate mixing during fuel dispense
Key Feature
Chemical resistant pump materials
End Equipment
Fuel dispensing equipment
Pump Function
Metering
Fluids
Corrosion inhibitors, lubricants, anti-icing additives, dyes, detergents, static dissipating additives
Flow Rate
0.5 to 10 L/min (7.9 to 159 USG/hr)
Differential Pressure
<40 psi (<2.76 bar)
Applications Overview
Fuel can be improved, changed or enhanced through the addition of fuel additives according to specific performance and usage requirements.
Additives can be added at the rack in a distribution terminal, at a service station style dispenser, or into the fuel stream dispensed from a delivery truck.
Typical examples include:
- Refining additives
- Detergent additives to keep fuel injectors clean
- Color dyes to identify fuel grades
- Lead-based additives for aviation
- Corrosion inhibitors
- Lubricants for extended engine and pump life
- Anti-icing additives for jet fuel
- Static dissipater additives
Micropump pumps deliver smooth, controlled flows of fuel additive into a fuel dispensing system.
PUMPING REQUIREMENTS
MICROPUMP SOLUTIONS
FLOW RATE: 0.5 to 10 L/min (7.925 to 158.5 USG/hr)
We have variable speed pumps for this application with flows from 0.131 to 13.9 L/min (2.1 to 221 USG/hr)
CHEMICAL RESISTANT TO HYDROCARBONS
Our chemically resistant construction materials stand up to the aggressive fluids found in fuel additives
PRECISE, METERED FLOW CONTROL
Our gear pumps with variable speed DC drives provide precise flow control
SMOOTH, PULSELESS FLOW
Gear pumps offer the virtually pulseless flow required for in-flow additive dispense
RELIABILITY
Our precision design and manufactured gears stand the test of rugged use
LEAK FREE
Our magnetic drives eliminates dynamic shaft seals, keeping fluid securely inside the pump and potential contaminants out
MAINTAINABILITY
We offer Service Kits for easy field serviceability
Performance Summary
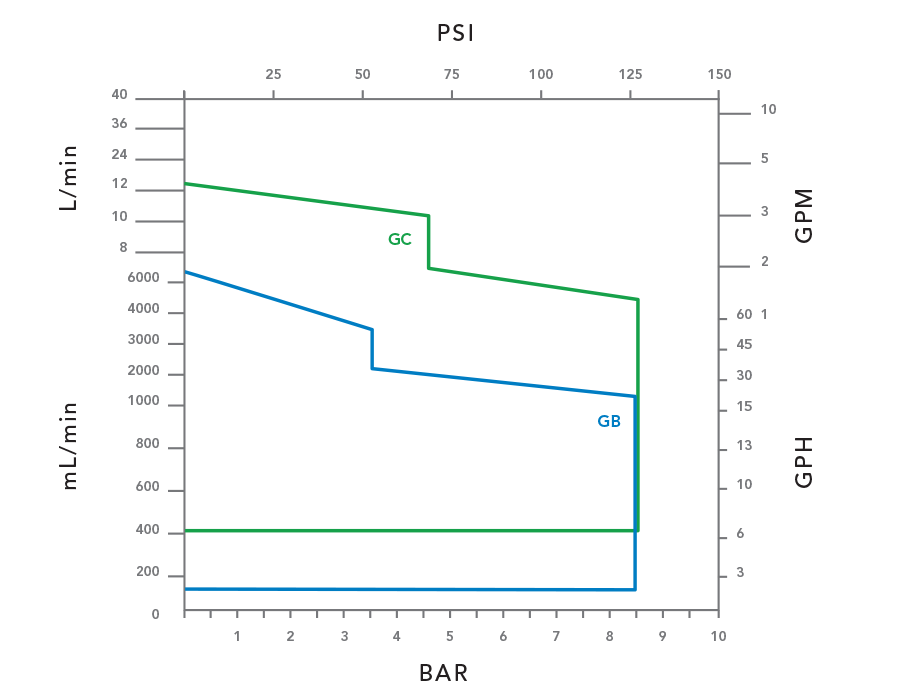
This chart indicates optimal operating ranges for recommended products.
Micropump Products Optimized for this Application
Micropump “suction shoe” style pumps are commonly used for this application. Series GB are best suited for lower flows, and Series GC for higher flows. Suction Shoe style gear pumps provide more consistent flow with varying differential pressure, and extended pump wear, than standard cavity style gear pumps. Suction shoe pumps also perform better with wide ranging temperature changes than cavity style pumps. Our integrated electromagnet EagleDrive™ provides variable, precise flow control in an energy efficient and compact package.
The Micropump Advantage
The unparalleled quality, performance record, reliability and long operating life of Micropump pumps and our extensive engineering expertise make Micropump a vital partner in this demanding market.
Headquarters
1402 NE 136th Avenue
Vancouver, WA 98684-0818 USA