Fuel Cell Technology
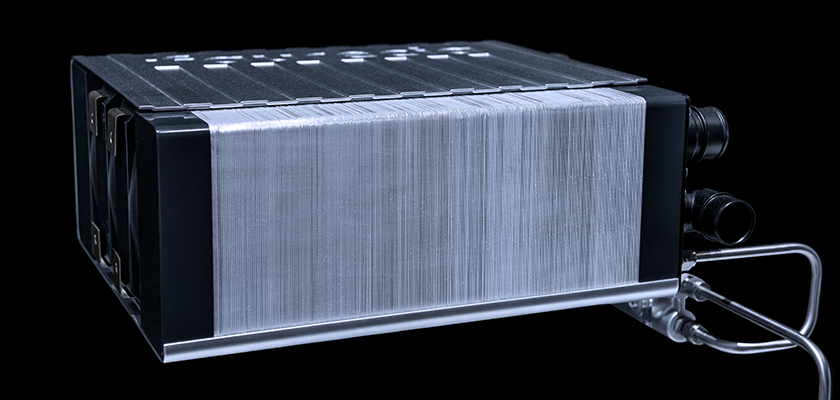
Application-Related Downloads
Application Summary
Application
Fuel Cell Technology
Description
Industry-leading fuel cell technology relies on pumps to move fluids for various aspects of fuel cell systems.
How It's Used
Pump fluid to improve the performance of fuel cell systems.
Key Feature
The operating performance required is essential to maintaining fuel cell differential pressure, accurate membrane hydration, precise flow rates, and long life for system uptime.
End Equipment
Integral components of systems from hydrogen generation technology to fuel cell systems for transportation, residential power, back-up power, micro-CHP or ancillary systems.
Pump Function
Circulation, Dosing, Metering and Transfer
Fluids
Liquid fuel, methyl alcohol, DI water, and water
Flow Rate
0.0085 to 6.8L/min
Differential Pressure
<17.2 Bar (250 psi)
Applications Overview
We have provided solutions to help solve problems for some of the earliest fuel cell systems globally. Ensuring exceptional performance and durability of our pumps, we are continually partnering for the next generation of technologies. Micropump pumps have been integral components of systems from hydrogen generation technology to fuel cell systems for transportation, residential power, back-up power, micro-CHP or ancillary systems. By partnering with us, you can leverage our decades of pump experience to achieve tailored fuel cell technology for vehicular or distributed power.
Micropump application engineers provide guidance in design and can work with you for customized component parts to optimize your system reliability. We have collaborated with technology leaders to improve various aspects of the fluid handling stages. From reformer efficiency through high differential pressures or initiating immediate fluid movement in the system based on control inputs, Micropump has delivered compact but robust designs. Micropump’s precision fluid movement includes handling water balance concerns of flooding or too dry conditions in the fuel cell stack. Due to our uniform and accurate flow rates, humidity management in the membrane is better controlled and more stable. The Micropump cavity and suction shoe gear style design also delivers high pressures for greater reformer efficiency and an isolated fluid path with no leak-prone dynamic seals.
When designing systems to power the future, choose Micropump as your partner.
PUMPING REQUIREMENTS
MICROPUMP SOLUTIONS
SYSTEM COST REDUCTION
Our pumps offer extended lifetime, system simplification.
ACCURATE PERFORMANCE
Our pumps feature excellent flow control and accuracy enabling efficiency and fast response for system control inputs.
SMALL PACKAGE SIZE
Our magnetic-drive gear pumps are small. When mounted to a Micropump electromagnetic EagleDrive™, we can offer a very compact pump and drive package.
LOW POWER REQUIREMENTS
We feature low parasitic load with the hydraulic and electrical efficiency of the mag-drive gear pump and EagleDrive, power requirements are very low.
MAINTENANCE EASE
Our pumps offer consistent performance even in fluctuating temperatures and can handle corrosive fluids.
Performance Summary
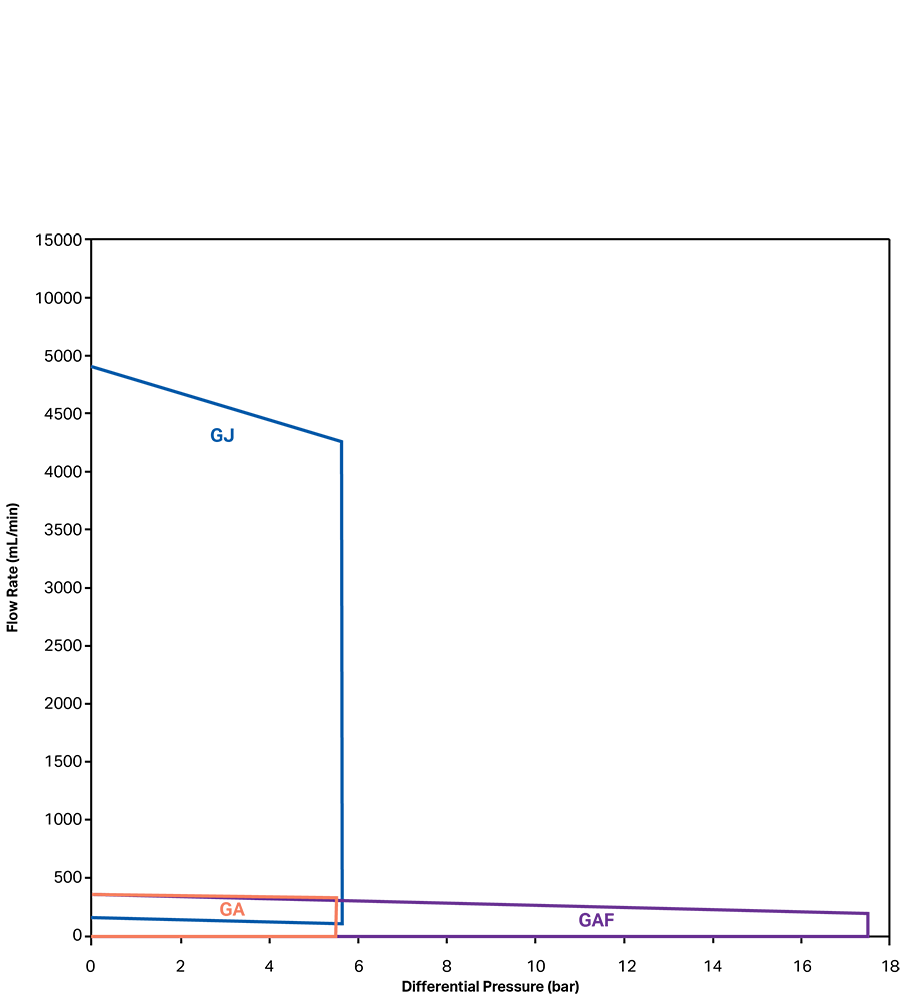
These charts indicate optimal operating ranges for recommended products.
Micropump Products Optimized for this Application
Micropump GA and GAF Series suction shoe style magnetic gear pumps and GJ Series cavity style magnetic gear pump are most commonly used in fuel cell applications.
The Micropump Advantage
The unparalleled quality, performance record, reliability and long operating life of Micropump pumps and our extensive engineering expertise make Micropump a vital partner in this demanding market.
Headquarters
1402 NE 136th Avenue
Vancouver, WA 98684-0818 USA