Gear Pump Repeatability
Gear Pump Repeatability
Back Leakage (Slip)
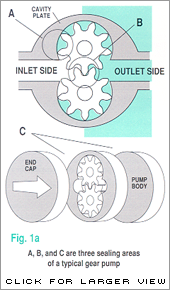
An important aspect of rotary gear pump performance is the dynamic sealing that takes place within the pump. This dynamic sealing allows the pumping parts to move while at the same time maintaining a distinct separation between the inlet and outlet. A gear pump has three such dynamic sealing areas: (A) the tips of the gear teeth and the cavity wall (either cavity plate or suction shoe), (B) where the gears mesh and close, and (C) the mating surfaces of the gears, the pump body, and the end cap (see Fig. 1a).
When all parts are assembled, these dynamic seals will be maintained at any position in the rotation of the gears. However, as with any dynamic seal, there must be clearances for the pumping parts to move. These clearances allow "back leakage" of the fluid from the high-pressure outlet side of the pump back to the low-pressure inlet side (see Fig. 2). Commonly referred to as “slip,” this recycled fluid trapped within the pump causes the pump's total flow rate (what comes out of the pump) to be less than the theoretical flow rate (what would come out of the pump if we could make the perfect, 100% efficient pump). Slip is the main factor in determining a pump's volumetric efficiency (Fig. 1b).
Pump Efficiency/Repeatability
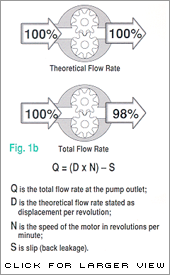
An important aspect of rotary gear pump performance is the dynamic sealing that takes place within the pump. This dynamic sealing allows the pumping parts to move while at the same time maintaining a distinct separation between the inlet and outlet. A gear pump has three such dynamic sealing areas: (A) the tips of the gear teeth and the cavity wall (either cavity plate or suction shoe), (B) where the gears mesh and close, and (C) the mating surfaces of the gears, the pump body, and the end cap (see Fig. 1a).
Now you may be thinking, “Why don't we run the appropriate tests, determine the amount of slip per pump, and provide you with the information?” The problem is that slip is not constant in gear pumps. There are several contributing factors that provide numerous possibilities, all of which can change the amount of slip for a given pump. The good news is there are several methods for detecting and compensating for these factors. First let's look at the factors in a pump application that may cause a variance in slip.
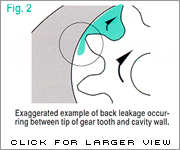
Differential Pressure
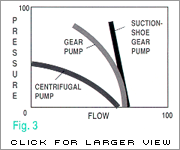
As differential pressure (difference between inlet and outlet pressure) increases, the amount of slip increases. Typically, fluids seek the path of least resistance; consequently, the higher the differential pressure, the more fluid will be forced back through the clearances (described previously), resulting in decreased flow rate. This is illustrated in Fig. 3. Notice how a pump's flow vs. pressure graph “curves” (flow rate decreases) as the differential pressure increases. This is also why positive displacement pumps have straighter curves than other less efficient pumps (see Fig. 3).
Micropump's suction-shoe-style gear pumps are pressure loaded, meaning differential pressure on the outlet side of the pump forces the sealing elements (suction shoe, gears, pump body) tighter together, making this type of gear pump more efficient (less slip) at higher differential pressures.
Therefore, in applications where the pump is subjected to varying differential pressure, slip may vary, and adjustments may need to be made to ensure repeatability.
Fluid Characteristics
- Viscosity/Fluid Shear A more viscous fluid will decrease the amount of slip for the simple reason that a thicker fluid is physically less capable of flowing back through the small clearances of the pump leak paths. The more viscous fluid, in effect, seals the leak paths, decreasing the amount of slip. Fluids, like water and oil, maintain viscosity (shear rate) under changing conditions. These fluids are called Newtonian fluids. On the other hand, the viscosity of fluids like catsup (a non-Newtonian fluid) will change under varying conditions. This change in the fluid's shear rate will cause pump slip to vary, to be difficult to predict, and may lower a pump’s ability to repeat.
- Mixed-phase Fluids Pumping mixed phase (fluid/gas) fluids lowers the repeatability of a pump. Mixed phase mixtures can take the form of homogeneous mixtures, separate liquid/gas flow, or slug flow. If the mixture is homogeneous or separated, slip is consistent and somewhat predictable. But if the flow rate is slug type (separate pulsed volumes of gas and liquid in the pumping cavity), slip values become high and varied. Obtaining a repeatable pump under these conditions is difficult at best!
In summary, when differential pressure and fluid conditions vary, slip will vary, and as a result, pump performance and flow rates become unpredictable. The answer is to compensate for this by monitoring pump performance and making adjustments as required. This can be done in several ways, depending upon the method most appropriate for your application.
Design & Manufacturing
Design tolerances and manufacturing capabilities play an important role in producing efficient rotary pumps consistently. Micropump uses a combination of gear and cavity materials that are manufactured to very close tolerances, producing pumps with smaller clearances. This results in efficient pumps with minimal slip.
Pump slip will eventually increase as a pump is used. This is caused by normal wear of the pump parts involved in the critical sealing areas as shown in Fig. 1.
Though our part tolerances are minimal, each part can be slightly different (± whatever the tolerance is) from a supposed identical part. Add together all the parts in the pump and these variables combine to produce pumps that will have slightly different flow rates per revolution. Consequently, two pumps run at identical speeds may not have identical output (see Fig. 4); however, whatever the output is, it will be consistent and repeatable, and the speed of the pump can be altered to deliver desired performance. Note the hypothetical example at right: pump #2 will deliver 100 cc consistently at 210 revolutions, while pump #1 delivers the same amount at 200 revolutions.
Fluid Sensing Devices (closed loop)
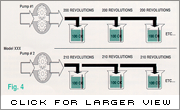
A fluid sensing device is an excellent method for monitoring pump performance. You can install a sensing device in the flow path to send feedback to the pump drive. Adjustments to the drive can then be made electronically to either increase or decrease the pump speed. Sensing devices can detect such fluid characteristics as flow rate, conductivity, acid content, viscosity, flowing mass of the pumped fluid, and fluid temperature. Selecting the proper control system is a vital step toward maintaining consistent flow rates and compensating for slip.
External By-pass Loop
This is a simple, mechanical method for controlling excess flow. The by-pass loop is installed into the system plumbing downstream from the pump outlet. The by-pass diverts a small portion of the total flow from the outlet back to the reservoir (see Fig. 5). The amount of flow diverted can be changed with a control valve or other similar device. For some applications, this is an effective, inexpensive way to attain a constant output.
Motor Speed
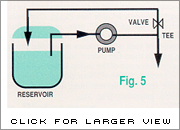
A gear pump's performance, being positive displacement, is ideally controlled by adjusting motor speed. Electronic feedback-back loops, such as a tacho generator, or an encoder (open loop), can be used to maintain constant motor speeds and provide predictable flow rates. As mentioned previously, a sensing device can be used to send electronic signals to increase or decrease motor speed. DC motors provide consistent speeds and are easily adjusted to compensate for wear. When practical, AC motors can be used with variable speed inverters to provide speed control.
Higher Speeds = Lower Slip%
A final note on pump slip: high-speed operation lowers the amount of slip as a percentage of total flow rate. Consequently, selecting a pump to deliver the desired flow rate at the highest speed that is still practical will reduce slip and its effects.
Flow Rate Repeatability
Flow rate repeatability can be achieved when the system, operating conditions, fluid parameters, and appropriate motor controls are evaluated to minimize and/or compensate for slip.
Find a Distributor
Get a Quote
Find a Product
Headquarters
1402 NE 136th Avenue
Vancouver, WA 98684-0818 USA